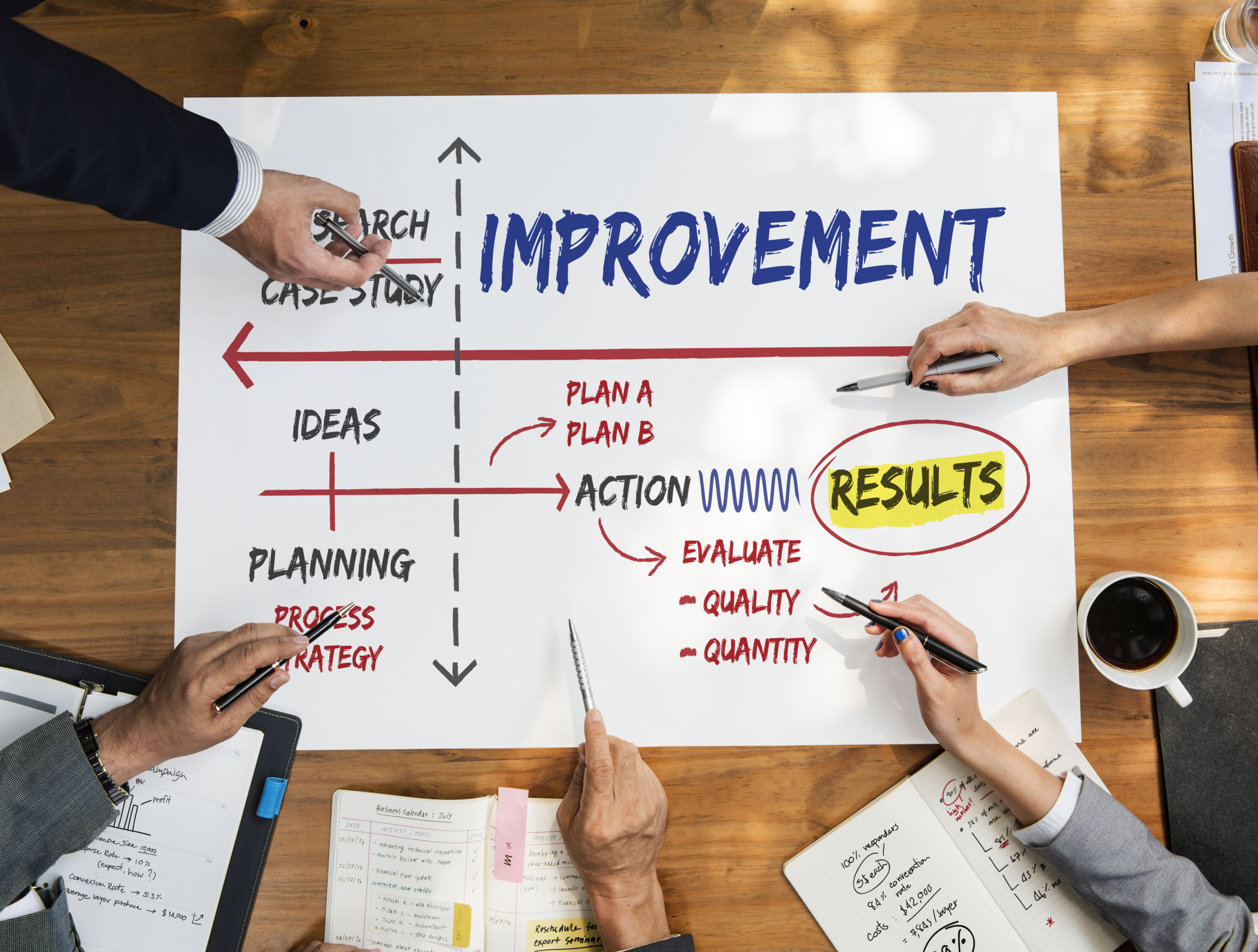
The Continuous Improvement Process Explained
In this article, we’ll give you continual improvement examples and techniques that will help you operate your business better.
In this article, we’ll give you continual improvement examples and techniques that will help you operate your business better.
A major function of a CAP (corrective action plan) is to prevent the same issues from occurring again. This leads to strengthened employee performances, products, and business processes to prevent errors that result in non-conformities. A CAP may for example address work instructions being misinterpreted, equipment failure, or a customer complaint.
People often use root cause analysis in everyday situations as one of many analysis methods without realizing it.
Non-conformance Reporting is a process used by companies to keep track of issues and problems. Once they find out what causes these, they can then put steps in place to prevent them from happening again. The process is documented using NCRs (Non Conformance Reports).
Although corrective action and preventive action are two important quality system elements, people often get confused about which type should be used when.
Whenever a “nonconformity” or incident happens in the workplace, management needs to take action to fix the problem.
In the context of an ISO 9001 Quality Management System (QMS), a nonconformity, also known as a non conformance, is failing to meet a requirement, realize and define the problem, contain the problem, determine its cause and take appropriate action to prevent it from happening again.